The D136-001-007 is a MOOG brand servo driver, also known as a servo controller. It is a device used to control servo motors, which can achieve high-precision motion control such as position, speed and acceleration.
MOOG is a well-known American motion control manufacturer whose products are used in a wide range of industrial machinery and automation equipment. As a servo driver of MOOG, D136-001-007 has the characteristics of stable performance, good controllability and fast response speed, which is suitable for various scenarios requiring high-precision motion control.
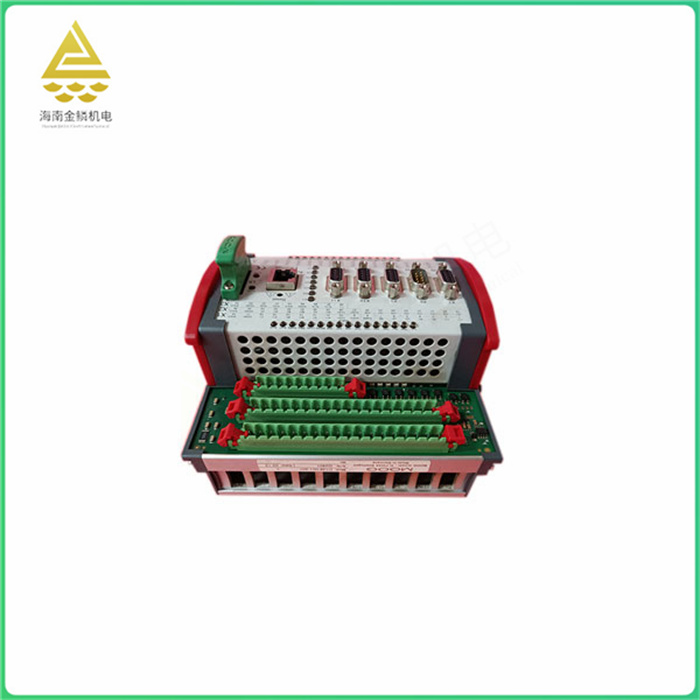
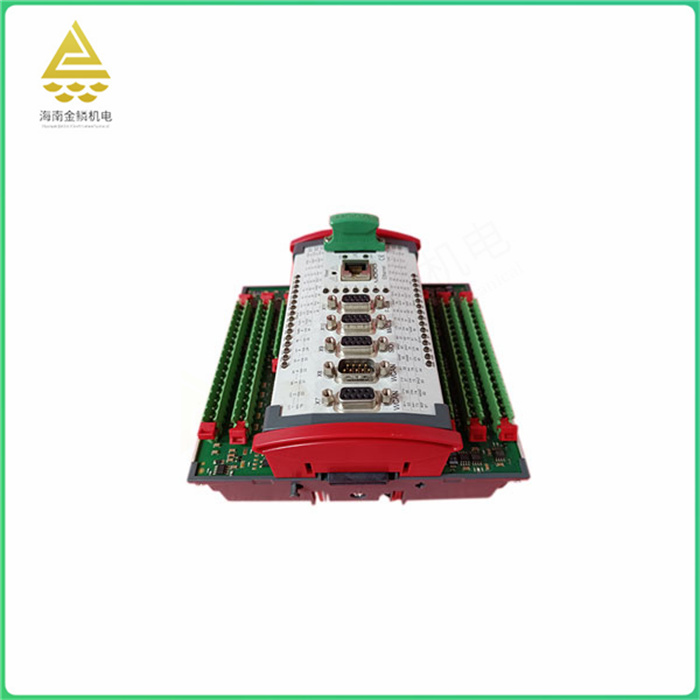
It should be noted that the selection and configuration of servo drivers need to be carried out according to the specific mechanical system and control requirements to ensure the stability and control accuracy of the system. At the same time, when using the servo drive, it is also necessary to comply with the relevant safe operating procedures and maintenance specifications to ensure the safety and reliability of the system.
A servo controller, also known as a servo amplifier or servo driver, is a controller used to control a servo motor. It is a part of the servo system and acts similar to the control of the inverter on the ordinary AC motor. The servo controller controls the servo motor by three ways: position, speed and torque, and achieves high precision positioning of the drive system. It is an important part of modern motion control, widely used in the field of injection molding machine, textile machinery, industrial robots and CNC machining centers and other automation equipment. In addition, the servo controller generally adopts the current, speed, position 3 closed-loop control algorithm based on vector control.
The servo controller has the following characteristics:
Stable operation: The servo motor control system can maintain a stable operating state, with high reliability and stability.
Good controllability: The servo motor control system has good controllability, and the operating state and characteristics of the motor can be changed by adjusting the control parameters.
Fast response: The servo motor control system has a fast response speed and can react and adjust quickly to external signals.
High sensitivity: The servo motor control system has a high sensitivity and can quickly respond to changes in the running state of the motor.
High precision: servo system accuracy is expressed in three forms: dynamic error, steady-state error and static error. The allowable deviation of the servo system is generally 0.01 ~ 0.001mm, and the deviation of the high-precision servo system can reach ±0.0001 ~ ±0.00005mm.
In short, the servo controller is an efficient, accurate and reliable controller for a variety of applications requiring high-precision motion control.
The main function of the servo controller is to control the motion and position of the servo motor. By receiving control signals (usually pulse signals or analog signals), it accurately controls the servo motor to achieve the required motion and position control.
Specifically, the servo controller can achieve the following functions:
Precise control of motor motion parameters such as position, speed and acceleration.
The output signal is adjusted to control the motor by comparing the feedback signal from the motor encoder or position sensor with the desired control signal.
To achieve high precision position control, speed control, force control and torque control and other motion control tasks.
Widely used in various automation equipment and industrial machinery, such as CNC machine tools, printing presses, robots, textile machinery, packaging machinery and so on.
It can improve production efficiency, reduce production costs, improve product quality and stability.
In short, as a high-precision motor control equipment, servo controller plays an important role in automated production.
The key of servo controller to realize high precision control lies in closed-loop control system and advanced control algorithm.
Closed-loop control system: The servo controller realizes high-precision control through the closed-loop control system. In a closed-loop control system, the servo controller receives the actual position feedback signal from the position sensor or motor encoder and compares it with the desired position. According to the comparison results, the servo controller adjusts the output signal to control the motor movement, so that the actual position gradually approaches the desired position. This closed-loop feedback mechanism can eliminate position errors and achieve high precision control.
Advanced control algorithms: Servo controllers are usually equipped with advanced control algorithms, such as PID control, vector control, etc. These algorithms can adjust the control parameters in real time according to the dynamic characteristics and load conditions of the motor and optimize the motor motion performance. For example, PID control can adjust the output signal based on the deviation of the actual position from the desired position, the rate of change of the deviation, and the integral value, thus achieving fast and accurate position control.
High-precision sensors and encoders: The servo controller uses high-precision sensors and encoders to detect the actual position and speed of the motor. These sensors and encoders are characterized by high resolution and high precision, and can provide accurate position and speed feedback information to provide reliable data support for closed-loop control systems.
Optimized mechanical structure: The mechanical structure of the servo motor also affects the control accuracy. By adopting high-precision bearings, low-friction materials and optimizing structural design, the mechanical error and friction resistance can be reduced, and the motion accuracy and stability of the motor can be improved.
Temperature control and compensation: the servo motor will generate heat during the working process, resulting in changes in the motor parameters, affecting the control accuracy. The servo controller is usually equipped with temperature detection and compensation functions, which can adjust the control parameters according to the change of the internal temperature of the motor, keep the motor in the best working state, and achieve high-precision control.
In short, the servo controller achieves high precision control through closed-loop control system, advanced control algorithms, high-precision sensors and encoders, optimized mechanical structure, temperature control and compensation measures.