Series M1
Component series 2X 1X
Rated pressure 160 bar
Piston -025.... 200 mm
Piston rod -0 14... 140 mm
. Travel length up to 3000 mm
The REXROTH servo drive TDM1.4-100-300-W1 servo system is one used for control
High-precision electronic equipment for motor movement, the main role is to precisely control the position, speed and acceleration of the motor
Motion parameters such as degree can realize various motion control tasks. Servo controllers usually use closed-loop control
In this way, the feedback signal from the motor encoder or position sensor is compared with the desired control signal
To adjust the output signal to control the motor. Servo controllers are widely used in various automation equipment
And industrial machinery such as CNC machine tools, printing presses, robots, textile machinery, packaging machinery and so on. here
In some equipment, the servo controller can achieve high precision position control, speed control, force control and torsion
Motion control tasks such as moment control, thereby improving production efficiency, reducing production costs, and improving product quality
And stability.
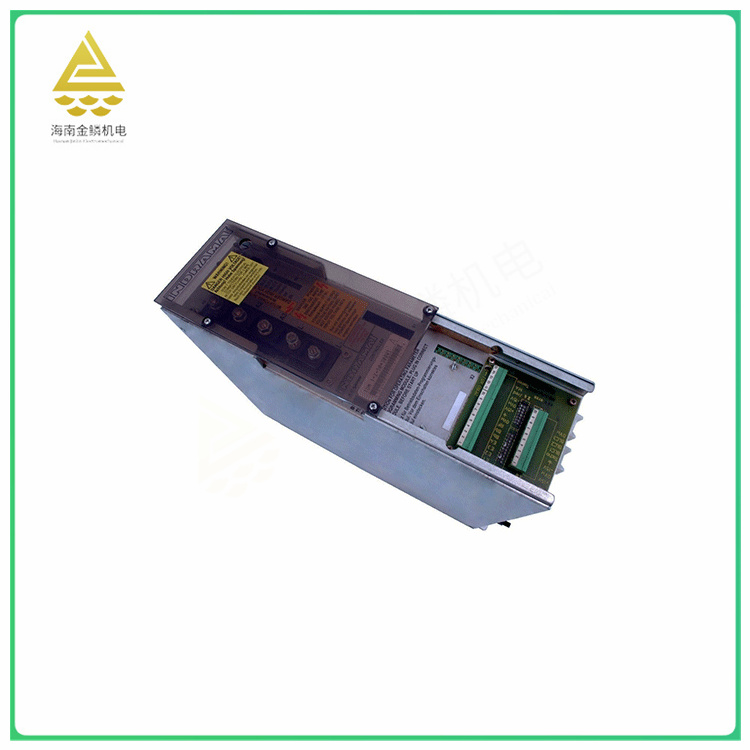
Torque direction:
The phase relationship between the three-phase system and the rotor magnetic field determines the direction of the torque and thus the polarity of the system deviation from the speed controller.
Control circuit signal regulation:
The speed controller compares the speed set value to the actual value from which the current set point is generated, which is fed to the current controller directed through the limiter circuit according to the rotor position (via BLC signal)
From the rotor position encoder), the current direction of the three stators is controlled by the winding so that the current generated in the stator is at its magnetic flux relative to the rotor is most advantageous. This relationship ensures that the torque and motor current are formed
Ratio. The motor current is controlled by the current controller. This is linked to the directional current controller to control the current in three in order to obtain a three-phase system with controlled amplitude, frequency and phase. Current controller output
The signal is timed at the pulse width modulation stage and amplified by a potential-free driver stage. The amplified signal used to drive the constructed three-phase bridge comes from six power transistors.

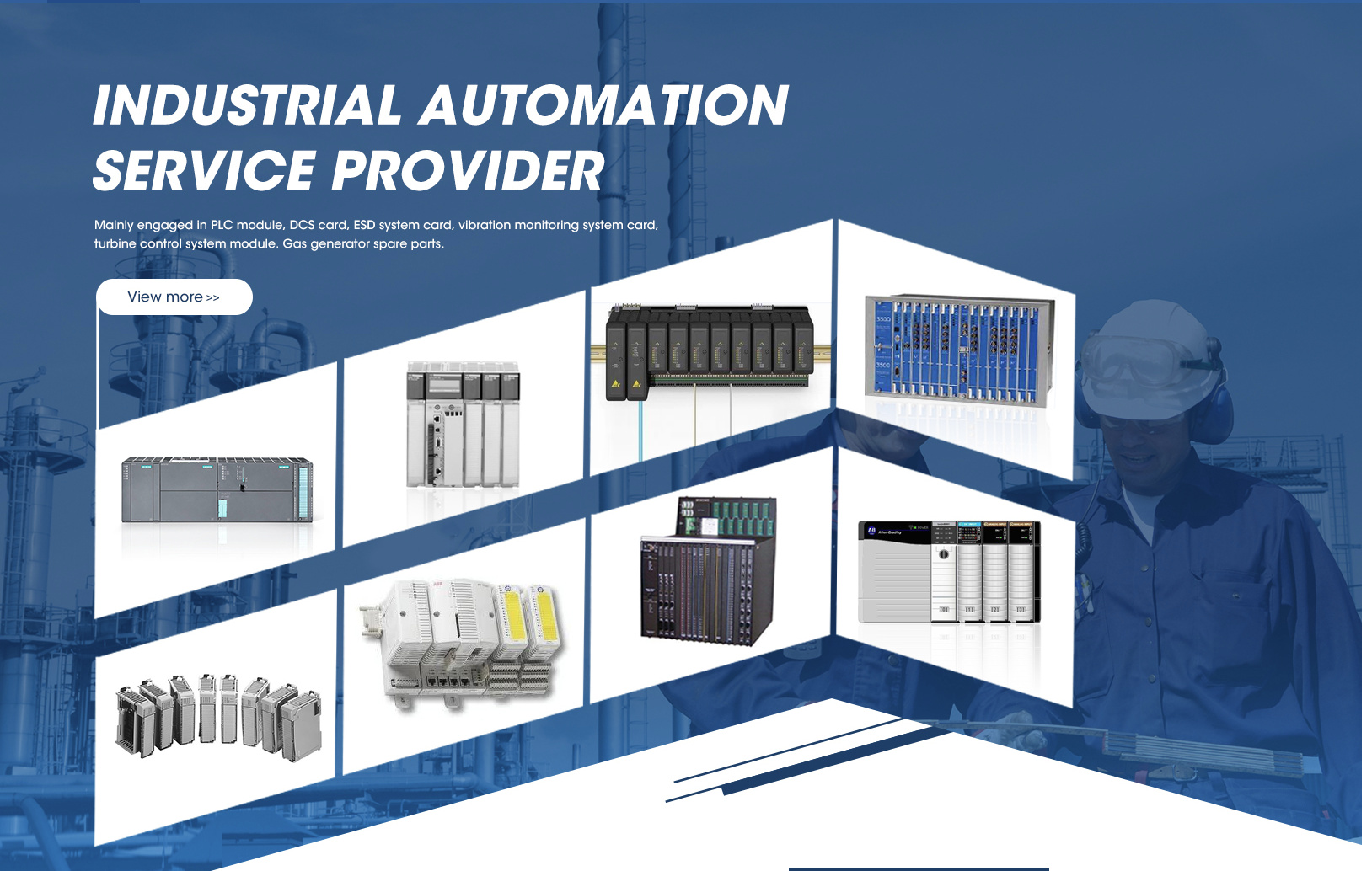